The Science Behind Porosity: A Comprehensive Overview for Welders and Fabricators
Understanding the complex mechanisms behind porosity in welding is critical for welders and makers aiming for impressive workmanship. From the composition of the base materials to the details of the welding procedure itself, a wide variety of variables conspire to either worsen or ease the existence of porosity.
Comprehending Porosity in Welding
FIRST SENTENCE:
Examination of porosity in welding reveals essential insights right into the honesty and high quality of the weld joint. Porosity, defined by the existence of dental caries or spaces within the weld metal, is a typical worry in welding procedures. These voids, if not effectively dealt with, can jeopardize the architectural integrity and mechanical properties of the weld, bring about possible failures in the completed product.
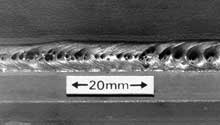
To detect and quantify porosity, non-destructive testing techniques such as ultrasonic testing or X-ray inspection are frequently utilized. These techniques enable the identification of internal flaws without jeopardizing the integrity of the weld. By evaluating the dimension, shape, and distribution of porosity within a weld, welders can make informed decisions to improve their welding processes and accomplish sounder weld joints.
Factors Influencing Porosity Formation
The incident of porosity in welding is affected by a myriad of variables, ranging from gas protecting efficiency to the ins and outs of welding criterion settings. Welding specifications, consisting of voltage, present, travel speed, and electrode type, also impact porosity development. The welding strategy employed, such as gas steel arc welding (GMAW) or secured steel arc welding (SMAW), can influence porosity formation due to variants in warmth distribution and gas coverage - What is Porosity.
Effects of Porosity on Weld Quality
Porosity development substantially compromises the structural stability and mechanical homes of welded joints. When porosity is existing in a weld, it creates spaces or cavities within the product, decreasing the general strength of the joint. These spaces act as anxiety focus points, making the weld more prone to breaking and failure under lots. The existence of porosity likewise deteriorates the weld's resistance to rust, resource as the entraped air or gases within the gaps can respond with the surrounding setting, bring about you can try this out degradation gradually. Furthermore, porosity can hinder the weld's ability to stand up to stress or impact, further threatening the total top quality and dependability of the welded framework. In essential applications such as aerospace, automotive, or architectural building and constructions, where safety and security and toughness are extremely important, the destructive effects of porosity on weld top quality can have serious effects, highlighting the relevance of decreasing porosity through proper welding techniques and procedures.
Methods to Reduce Porosity
To enhance the top quality of welded joints and make sure structural integrity, welders and producers employ particular techniques targeted at reducing the formation of spaces and tooth cavities within the material during the welding process. One effective technique to reduce porosity is to ensure appropriate product preparation. This includes thorough cleansing of the base metal to remove any type of contaminants such as oil, oil, or moisture that could add to porosity development. Furthermore, utilizing the appropriate welding parameters, such as the right voltage, current, and travel rate, is vital in stopping porosity. Preserving a constant arc size and angle throughout welding likewise helps in reducing the possibility of porosity.

Using the suitable welding technique, such as back-stepping or utilizing a weaving activity, can also aid disperse heat evenly and reduce the opportunities of porosity development. By executing these methods, welders can properly reduce porosity and produce top notch bonded joints.
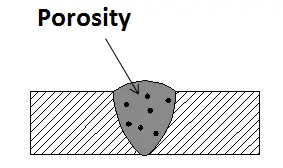
Advanced Solutions for Porosity Control
Executing cutting-edge innovations and ingenious approaches plays a crucial function in attaining premium control over porosity in welding processes. One advanced solution is the usage of sophisticated gas combinations. Securing gases like helium or a mix of argon and hydrogen can aid reduce porosity by providing better arc security and enhanced gas insurance coverage. Furthermore, employing advanced welding techniques such as pulsed MIG welding or changed atmosphere welding can additionally help minimize porosity problems.
Another innovative remedy involves using innovative welding devices. For circumstances, utilizing equipment with integrated attributes like waveform control and innovative source of power can boost weld quality and reduce porosity risks. The execution of automated welding systems with specific control over criteria can significantly reduce porosity issues.
In addition, incorporating innovative monitoring and examination modern technologies Related Site such as real-time X-ray imaging or automated ultrasonic screening can aid in discovering porosity early in the welding procedure, enabling for prompt rehabilitative activities. In general, incorporating these sophisticated services can significantly improve porosity control and enhance the total high quality of welded parts.
Final Thought
In verdict, comprehending the science behind porosity in welding is important for welders and makers to create high-quality welds - What is Porosity. Advanced services for porosity control can better enhance the welding process and make certain a strong and dependable weld.